The Ultimate Guide To Alcast Company
The Ultimate Guide To Alcast Company
Blog Article
What Does Alcast Company Mean?
Table of ContentsThe Only Guide to Alcast CompanyNot known Incorrect Statements About Alcast Company Everything about Alcast CompanyThings about Alcast CompanyHow Alcast Company can Save You Time, Stress, and Money.Facts About Alcast Company Revealed
Chemical Contrast of Cast Light weight aluminum Alloys Silicon promotes castability by reducing the alloy's melting temperature level and enhancing fluidity during spreading. Furthermore, silicon contributes to the alloy's toughness and use resistance, making it important in applications where sturdiness is essential, such as automotive components and engine parts.It additionally improves the machinability of the alloy, making it simpler to process right into completed items. In this method, iron adds to the overall workability of light weight aluminum alloys. Copper increases electrical conductivity, making it helpful in electrical applications. It additionally improves corrosion resistance and includes in the alloy's general stamina.
Manganese adds to the toughness of light weight aluminum alloys and boosts workability (aluminum casting company). It is commonly made use of in wrought aluminum products like sheets, extrusions, and profiles. The presence of manganese aids in the alloy's formability and resistance to splitting throughout fabrication procedures. Magnesium is a light-weight element that offers strength and impact resistance to aluminum alloys.
Getting The Alcast Company To Work
Zinc boosts the castability of light weight aluminum alloys and aids control the solidification process during casting. It enhances the alloy's strength and firmness.
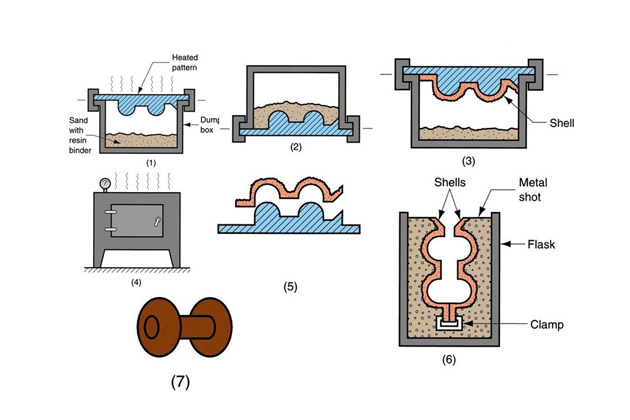
The primary thermal conductivity, tensile strength, yield toughness, and elongation vary. Amongst the above alloys, A356 has the highest thermal conductivity, and A380 and ADC12 have the most affordable.
8 Simple Techniques For Alcast Company
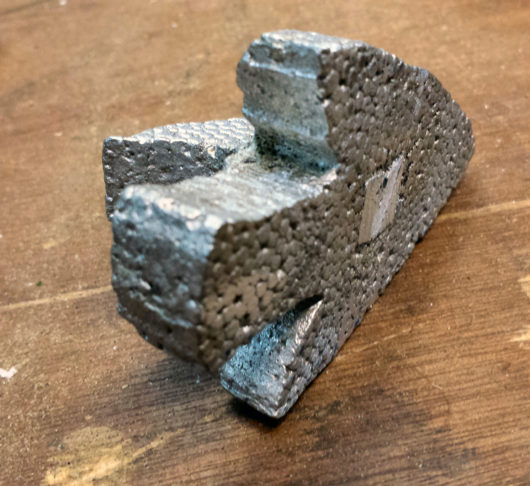
In precision casting, 6063 is fit for applications where intricate geometries and top notch surface area coatings are paramount. review Examples include telecommunication rooms, where the alloy's superior formability permits streamlined and cosmetically pleasing styles while preserving structural honesty. In the Illumination Solutions sector, precision-cast 6063 elements create classy and reliable illumination fixtures that require elaborate shapes and good thermal performance.
It results in a finer surface area coating and better corrosion resistance in A360. The A360 exhibits remarkable elongation, making it suitable for complex and thin-walled parts. In precision spreading applications, A360 is well-suited for markets such as Customer Electronics, Telecommunication, and Power Devices. Its enhanced fluidity permits elaborate, high-precision parts like smartphone coverings and communication tool housings.
3 Easy Facts About Alcast Company Described
Its one-of-a-kind homes make A360 a valuable selection for precision spreading in these sectors, improving product sturdiness and high quality. aluminum casting manufacturer. Aluminum alloy 380, or A380, is an extensively utilized casting alloy with numerous unique qualities.
In accuracy spreading, aluminum 413 shines in the Consumer Electronic Devices and Power Equipment markets. This alloy's premium deterioration resistance makes it an excellent option for exterior applications, guaranteeing lasting, long lasting items in the stated sectors.
Alcast Company for Beginners
As soon as you have actually determined that the light weight aluminum pass away casting process is appropriate for your project, an important next action is choosing one of the most proper alloy. The light weight aluminum alloy you select will considerably affect both the casting process and the homes of the last product. Due to this, you need to make your choice thoroughly and take an informed technique.
Establishing one of the most suitable light weight aluminum alloy for your application will mean evaluating a broad array of features. These relative alloy attributes comply with the North American Die Spreading Association's standards, and we've separated them into two groups. The initial group addresses alloy features that influence the production procedure. The 2nd covers features affecting the residential properties of the end product.
All About Alcast Company
The alloy you pick for die spreading straight influences several elements of the spreading procedure, like exactly how simple the alloy is to collaborate with and if it is susceptible to casting flaws. Warm fracturing, also referred to as solidification breaking, is a common die casting problem for light weight aluminum alloys that can cause internal or surface-level splits or fractures.
Particular light weight aluminum alloys are extra susceptible to hot fracturing than others, and your choice needs to consider this. One more common defect discovered in the die casting of light weight aluminum is die soldering, which is when the cast sticks to the die walls and makes ejection challenging. It can damage both the actors and the die, so you must search for alloys with high anti-soldering buildings.
Corrosion resistance, which is currently a remarkable attribute of light weight aluminum, can vary considerably from alloy to alloy and is a crucial particular to consider depending upon the environmental problems your item will certainly be exposed to (Aluminum Casting). Put on resistance is one more building frequently sought in light weight aluminum products and can differentiate some alloys
Report this page